
Poured-In-Place Playground Surfacing System
​
Delivery, Storage & Handling
Storage and Protection: Store materials protected from exposure to harmful
environmental conditions and at a minimum temperature of 40 degrees F (4
degrees C) and a maximum temperature of 90 degrees F (32 Degrees C).
​
Project/Site Conditions
Environmental Requirements: Install surfacing system when the minimum
ambient temperature is 40 degrees F (1 degree C) and maximum ambient
temperature is 90 degrees F (32 degrees C). Do not install in steady or heavy rain.
​
Products
​
Specifier Note: The Type of playground equipment determines the required
thickness and the thickness may be different at various locations on the playground
site. Depending on ASTM F1292 requirements for critical fall height.

Thickness CFH
1 3/4" 4"
​
2" 5"
​
2 1/2" 6"
​
3" 7"
​
3 1/2" 8"
​
4" 9"
​
4 1/2" 10"
​
5" 12"
​
6" 13"
Site Preparation
​
There are many different applications in which EPDM can be poured. It can
be applied over a subsurface of concrete, asphalt or crushed stone.
​
Concrete
Requires minimum thickness (which will typically be 4”) for non-weight
bearing loads per the standard. 2% slope is recommended as well as broom finish.
New concrete must be fully cured up to 2 days.
​
Asphalt
Requires minimum thickness (which will typically be 2”) for non-weight
bearing loads per the standard. A 2% slope is recommended. New asphalt must be
cured up to 30 days.
​
Crushed Stone
Stone for the base must be a homogeneous mix of .” stone down to fines
and you need to achieve a 95% compaction.
The minimum depth of the crushed stone base is 4”. Typical thickness
ranges from 4’-6”. Crushed stone base layers thicker than 6” are more challenging
to achieve the necessary 95% compaction rate throughout the base. The thickness
must never exceed 10”.
Crushed stone base must be fully contained.
A 2% slope is recommended.
Crushed stone is not an acceptable sub-base for any mounded area. In these
areas, in order to make it more stable, the stone would need to be skim-coated with
concrete or asphalt.
​
Note: Regardless of the base option you select for safety surfacing, proper drainage
will be critical in order for the surfacing system to last for a long time. Drainage
that is not adequate will cause premature breakdown of the poured or tile material
in affected areas and will cause the warranty to be voided.
​
Please view the pictures below to view installation process :


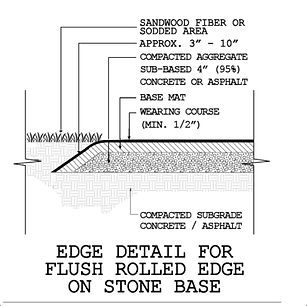

Required mix proportion by weight
​
Basemat: 16+% urethane. 14% urethane, 86% rubber.
Top Surface: 22% urethane, 78% rubber (based on entire rubber & urethane mix).
​
Installation
​
Basemat Installation
1. Using screeds and hand towels, install the basemat mixing on a mortar mixer
to the specified thickness. Required 16% Urethane + 84% rubber.
2. Do not allow foot traffic or use of the basemat surface until it is sufficiently
cured.
​
Top Surface Installation
1. Using a hand towel and a screen bar, install top surface at mixing on a
mortar mixer 22% Urethane, 78% EPDM or TPV to a normal thickness of
.”.
2. Allow the top surface to cure for a minimum of 48 hours.
3. At the end of the minimum curing period, verify that the top surface is
sufficiently dry and firm to allow for traffic and use without damage to the
surface.
4. Do not allow foot traffic or use of the surface until it is sufficiently cured.
​
Specifier Note: Specify provisions for protecting work after installation but prior to
acceptance by the owner.
​
Protect the installed playground surface from damage resulting from subsequent
construction activity on the site.
​